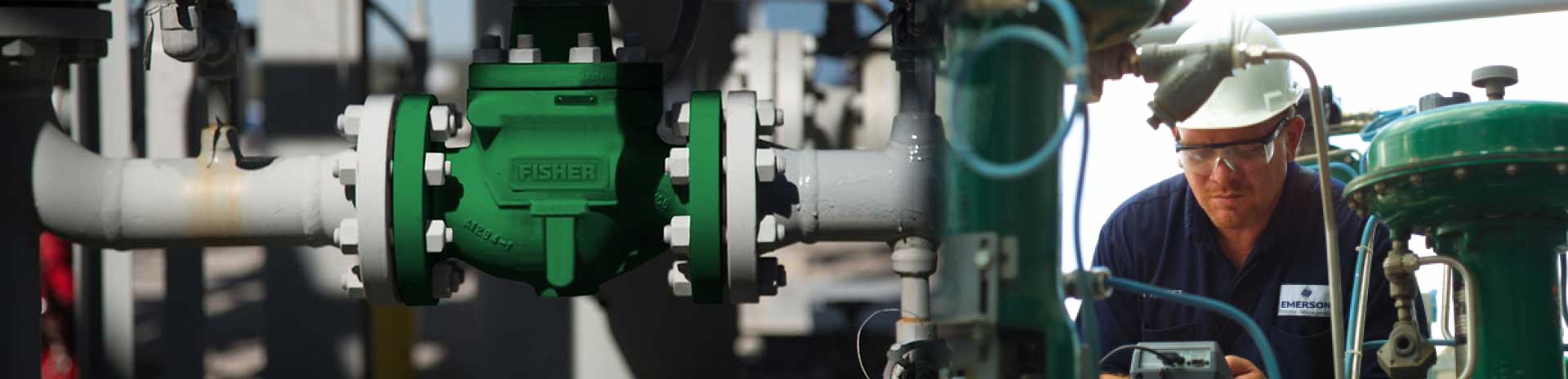
Oversizing Valves amplifies their problems unto the process
Often, valves are oversized for the given operating conditions. Generally, if a valve spends the majority of its life at less than 25% open and the measurement signal is greater than say 50% of span, one can conclude that the valve is oversized. This means that a small change in the valve position causes a large process swing. Apart from the obvious wear and tear on the valve due to the high pressure drop (and potential cavitation), a large amount of the pumping horsepower is wasted as well. Moreover, oversizing valves can also have negative impact on controls as well. Due to the high sensitivity of the process, small valve problems, such as stiction and backlash will translate into large problems in the process itself. Essentially, oversized valves “amplify” their problems unto the process. For example, a seemingly small 1% stiction problem on a valve will translate into a 3% problem in the process.
On the other side of the spectrum, there are cases where valves are undersized. In this case, large valve changes cause a small “dent” in the process. These valves tend to spend most of their lives either completely open or closed, thereby negating the use and investment of a control valve.
One of my first jobs after graduation from university was with a large multi-disciplinary engineering firm. This firm designed processes for many different industries, including pulp and paper, I worked in the instrumentation and control department. During my first project, I was given the task of sizing a control valve. Being an electrical engineer, this was new, exciting, and somewhat alien to me. Using a standard valve-sizing program, I entered all the necessary information such as the pressure drop, minimum and maximum flows. The valve-sizing program told me that a four-inch ball valve would do the job. For the given conditions, the valve would operate in the “sweet spot”, that is between 40% and 60% open.
a seemingly small 1% stiction problem on a valve will translate into a 3% problem in the process.
Since that was the first time I had sized a valve, I decided to have my department supervisor check my results. Stepping into his office, I saw that the project manager was there as well. I handed my supervisor my results; he looked at my results, and nodded approvingly. He then gazed upward in a philosophical nature and said “You know what, instead of putting in a four-inch valve, let’s put in a six-inch valve – just to be safe!” I readily agreed. After all, being the rookie that I was, what did I know about valve sizing? Not to be outdone, the project manager boasted “Let’s put in an eight-inch valve. That way we can tell our client that instead of building them a 600 tons-per-day mill, we built them an 800 tons-per-day mill.”
This ‘over engineering mind set’, when it comes to valve sizing, had an negative impact on the operation of the mill during start up and subsequent years.
It was during that start up that I discovered that, when it comes to control valves – size matters!