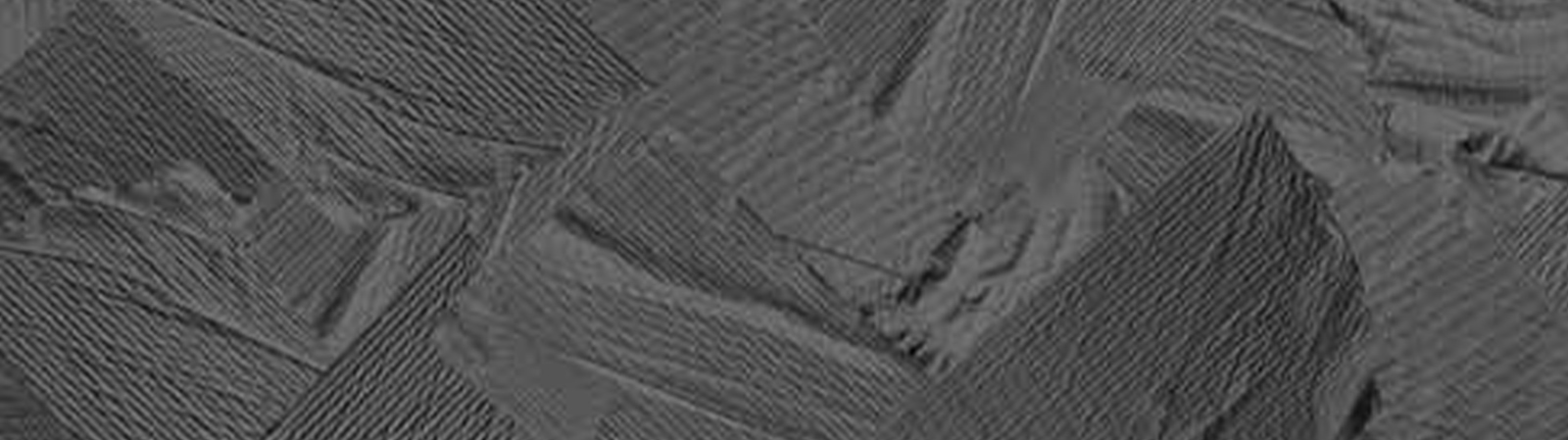
Discovering Record Setting Backlash in an Operating Control Valve
At the mid-morning mark, I wrapped up the first lecture; it covered identifying and measuring process dynamics, as well as control valve troubleshooting techniques. Next, I asked my class to choose a loop on which we could test and apply our new-found knowledge. The result of this test would then be used later on to actually tune the loop. After some searching and debating, one of my students suggested (with a certain gleam in his eyes) a control loop that we could use. The “guinea pig” loop in this case was a cleaner pressure control loop. A cleaner is a cone-shaped piece of process equipment used in the pulp and paper industry. It removes heavy particles, such as sand, from pulp stock through centrifugal action; thereby “cleaning” it. The efficiency of a cleaner is affected by inlet pressure variations and consequently, differential pressure variations across the said cleaners.
After setting up a fast trend on the DCS (one second update), we put the controller in manual mode and proceeded to perform bumps on the output. A series of 1% changes proved to be fruitless, the pressure did not react. We then graduated to 5% bumps, still nothing. Only when we made 10% changes did we see a change in the pressure. It was clear that this valve was ill. We made several more changes in the same direction, and the pressure did react as expected. I began to suspect what sort of illness was afflicting the valve. In order to prove my theory, we reversed the direction of the step changes. This time, the pressure did not react. In fact, we had to move the controller output a total of 30%, in the opposite direction, in order to see a change in the pressure. I asked my students what kind of sickness the valve had, and they all made me proud by answering “backlash!”.
…process control audits have revealed that one third of all control related problems are due to faulty valves. There are no controller tuning methods that will compensate for a bad valve.
Backlash is one of two major “diseases” that will adversely affect valves. The other valve “sickness” is known as “stiction” – short for static friction. Backlash occurs when a valve has some looseness or “slop” in its linkages. It can be present in the valve positioner, actuator or its linkages. This looseness translates into lost valve precision, which in turn affects control efficiency. Stiction, on the other hand, is caused by friction in the valve assembly. This friction can be present in the valve packing, the actuator, the valve body, and even in the positioner. It is important to note the occurrences of backlash and stiction are not necessarily mutually exclusive. Faulty valves have a direct negative impact on controller efficiency; a valve must be precise within 1% of change. In fact, process control audits have revealed that one third of all control related problems are due to faulty valves. There are no controller tuning methods that will compensate for a bad valve.
But what could be causing such large amount of backlash? The only way to find out was to physically inspect the valve. As we trooped out of the control room into the bowels of the mill, I mentally went through the list of “the usual suspects”: rack-and-pinion actuators and loose feedback connections between the valve stem and the positioner. After some searching, we finally laid eyes on the valve. The valve in question was a ball valve with a diaphragm actuator. In this type of valve, the actuator provides linear “up-down” motion. This “up-down” motion is then transformed into rotary motion via a lever arm that is connected to the valve shaft and ball.
What I saw next has, to this day, etched my mind. The pin that connected the lever arm to the actuator was missing. In its place was a mesh of electrical wire and – you guessed it- duct tape! The whole knotted mess was holding on for its dear life, in spite of the record holding amount of backlash (still unbroken in 30 years).
At that moment, someone quipped, “I guess that’s one more use for duct tape”.