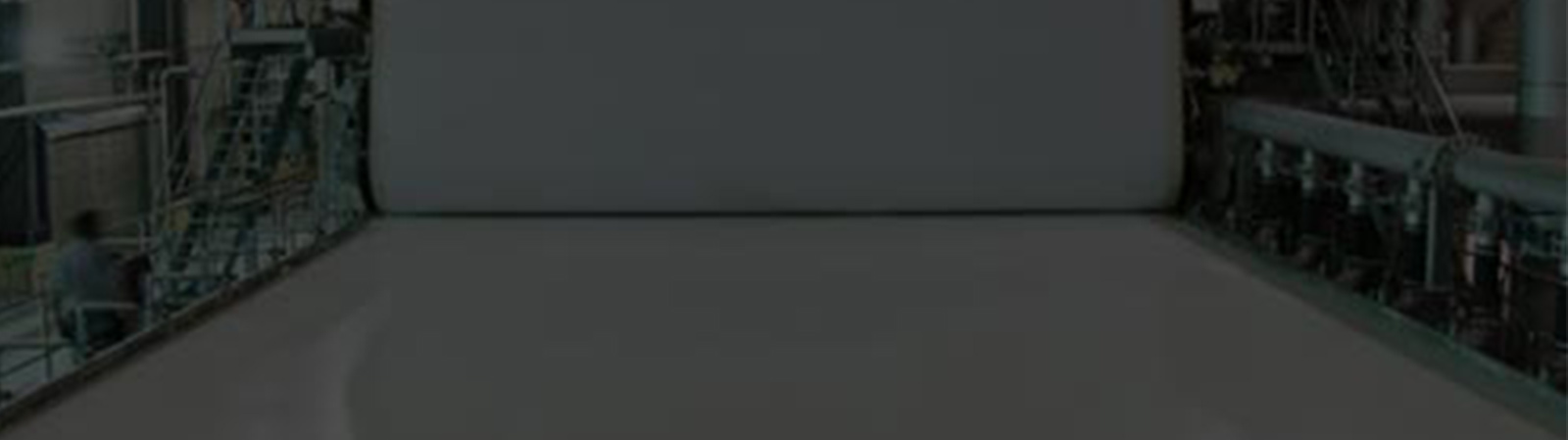
Excessive transmitter damping hides mechanical design fault
I firmly believe that, given a set of initial conditions (and enough time), everything will gravitate towards their natural state. In this adventure, I was once again giving a loop tuning/troubleshooting lecture in the field.
My students and I were hooking up my data logger to the input and output signals of a control loop. The loop in question was in the stock preparation area of a paper mill, a stock flow controller feeding a screen. A screen is designed to remove particles from the pulp stock based on size. Large flow and consistency (pulp concentration) swings can cause the screen to plug up. The only way to unplug the screen is to shut down that part of the process and manually ‘scrape’ out the screen. This is a costly and disruptive operation. In this case, the flow meter was a magnetic flow tube type, a flow tube measures the velocity of the fluid in the pipe, thereby inferring the flow. The valve was a six-inch, ‘V-Ball’ type.
Once hooked up to the flow control loop, we proceeded to perform bump tests on the loop. That is when things turned very interesting: every time the output was bumped, the flow responded in a “smooth” fashion, taking 60 seconds to settle out. This response was so “clean”, so “smooth” and perfect that even theory would be challenged to reproduce such a response. I knew that nature itself is never so accommodating, so something was afoot.
I asked my class whether it made sense that an in-compressible stock flow would take 60 seconds to settle out, given the fact that the valve was only 6 inches. They all responded “No”, it did not make sense. I then asked them what could be causing such a slow response, one answered “transmitter damping” (the linear thinker) and another answered “the valve” (the lateral thinker).
Every time the output was bumped, the flow responded in a “smooth” fashion, taking 60 seconds to settle out.
The next step was to check the damping setting in the transmitter. We knew that the damping had to be in the transmitter since we were measuring the signal directly from the transmitter itself. Damping is typically applied in transmitters or controllers in order to remove noise from the signal. People seem to have an aversion to noise and prefer to see straight lines on their process trends.
After some lengthy navigation through the cryptic menus in the flow transmitter, we finally arrived at the transmitter damping setting: it was set at fifteen seconds. I typically consider two seconds more than enough for a flow, let alone fifteen seconds! Such a large amount of damping not only masks any noise in the signal, it also hides the actual process dynamics. But the question remained: why would someone put such a large amount of damping in the transmitter? What was their reasoning (for everything happens for a reason)? “Obviously, there must be a lot of noise on the signal” one of my student said. I then asked a more fundamental question: why was there excessive noise on the flow signal? No one could immediately answer that question. We proceeded to go out and physically inspect the installation of the flow tube itself.
Upon examining the installation of the flow tube, our question was promptly answered. The flow-tube was flanged to a piping elbow. Moreover, the control valve was less than 12 inches downstream of the tube. Magnetic flow tube flow meters require a stable plug flow in order to develop a stable, clean and reliable signal.
Any source of fluid turbulence such as elbows, tees and valves will affect the flow stability and cause signal noise. In this case, every possible rule and guidelines for installing a magnetic flow transmitter was broken. Consequently, the solution to cover up for a mechanical design fault was to put excessive damping in the transmitter.
See No Evil, Hear No Evil, Speak No Evil…